NOx-arme Kessel der nächsten Generation Brenner Nachrüstungen - Leistung und Überlegungen in der Praxis
KATEGORIEN:
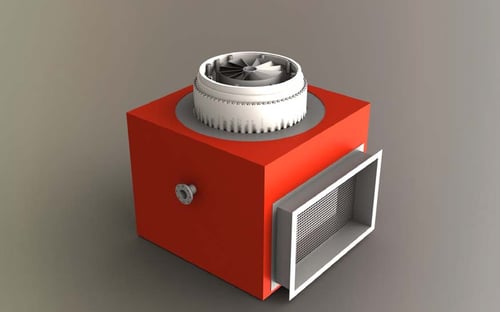
Im Jahr 2006 kaufte die Raffinerie von Valero Corpus Christi in Texas Zeeco® GLSF Free-Jet Next Generation Ultra-Low NOx Brenner für zwei Kessel, um die Emissionsvorschriften zu erfüllen. Diese Kessel waren in Konstruktion und Betriebsbedingungen identisch. Die GLSF Free-Jet Brenner boten die wirtschaftlichste Option zur Einhaltung der Emissionsvorschriften, da sie keine externe Rauchgasrückführung (EFGR) benötigen. Jeder Kessel ist über 70 Jahre alt, und die Nachrüstung von Brennern mit extrem niedrigen Emissionen ohne EFGR zur Erfüllung der strengen Emissionsanforderungen war eine Herausforderung.
Abstrakt
Brenner Nachrüstungen in Industriekesseln sind eine wirtschaftliche Lösung, um niedrigere NOx-Werte mit bestehenden befeuerten Anlagen zu erreichen. Die Entwicklung einer ultra-niedrigen NOx Brenner Grundfläche der nächsten Generation, die in einen bestehenden Brenner Ausschnitt passt, stellt jedoch in vielen Anwendungen weiterhin eine Herausforderung dar. Die Entwicklung eines Brenner mit einem Flammenmuster oder -profil, das innerhalb des vorhandenen Platzes und der begrenzten Brennerlänge an der Rückwand betrieben werden kann und dennoch eine signifikante NOx-Reduzierung erreicht, hat sich ebenfalls als schwierige Aufgabe erwiesen.
Zeeco hat eine patentierte, ultra-niedrige NOx-Free-Jet-Technologie der nächsten Generation Brenner mit einer kompakten mechanischen Grundfläche entwickelt. Der GLSF Free-Jet Brenner erzeugt ein Flammenprofil mit sehr begrenzter Flamme-zu-Flamme-Wechselwirkung für Installationen mit mehreren Kesseln Brenner und erreicht gleichzeitig kürzere Flammenlängen.
Eines der anderen Hauptanliegen für die Betreiberfirma des Endverbrauchers sind die Gesamtbetriebskosten für ultra-niedrige NOx-Brenner der nächsten Generation. Sie können im Vergleich zu konventionellen Emissionskesselbrennern höhere Wartungskosten verursachen. Zeeco bietet das wartungsärmste Design auf dem Markt bei ähnlichen NOx-Emissionsergebnissen. In diesem Beitrag werden diese Konstruktionsdetails, spezifische Details der Nachrüstungsinstallation und die Erfahrungen, die bei der Nachrüstung bestehender Kesselbrenner in der Corpus Christi Raffinerie von Valero gemacht wurden, einschließlich der Auswirkungen auf die Nebenluft, sowie die Ergebnisse von Emissionsprüfungen vor Ort für mehrere Nachrüstungsanwendungen erläutert.
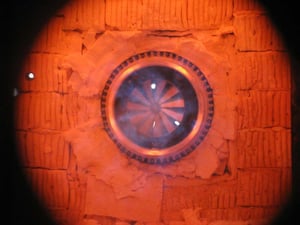
Ursprüngliche Konstruktionsbedingungen
Jeder Kessel war mit zwei konventionellen Brennern ausgestattet. Die Informationen zu den Kesseln waren aufgrund des Alters der Anlage begrenzt, und viele der Details in Bezug auf die Nachrüstung der nächsten Generation Brenner waren vor 70 Jahren nicht wichtig und daher nicht eindeutig dokumentiert. Außerdem fehlten einige der ursprünglichen Konstruktionsunterlagen. Zeeco ersetzte jeden der vorhandenen konventionellen Brenner durch einen Zeeco GLSF Free-Jet Brenner. Die Wärmeabgabe der neuen Brenner wurde auf 77,4 MM Btu/hr pro Brenner festgelegt. Der Druckabfall der Verbrennungsluft wurde auf 3,25" W.C. bei 15 % Luftüberschuss und einer Lufttemperatur von 100° F festgelegt.
Die neuen Brenner wurden so ausgelegt, dass bei Bedarf 0,3 lb Dampf/lb Brenngas in den Brenngasstrom eingespritzt werden können, um die NOx-Reduktion zu erhöhen, da EFGR für diese Anwendung nicht geplant war. Die Verwendung einer kleinen Menge Dampf war weniger kostspielig als die Überarbeitung des Kessels, um ca. 14% EFGR hinzuzufügen, um den geforderten NOx-Emissionswert von 0,03 lb/MM Btu (HHV) zu erreichen.
Die neuen Brenner wurden in der bestehenden Brenner Windbox-Konfiguration installiert. Die neue Brenner Grundfläche war ungefähr gleich groß wie die der vorhandenen Brenner, so dass die Kesselmodifikationen für die Brenner Installation minimiert wurden, um die Gesamtinstallationskosten der Nachrüstung zu reduzieren.
Schlussfolgerung
Die Nachrüstung der Kessel war aufgrund des Alters der Kessel und des Umfangs der für die Anwendung verfügbaren Informationen eine große Herausforderung. Nachdem die Herausforderungen erkannt und angegangen worden waren, konnten die Kessel jedoch die geforderten 0,03 lb/MM Btu NOx-Emissionen und 50 ppmv CO-Emissionen ohne den Einsatz von EFGR erreichen. Durch den Einsatz der Free-Jet-Mischtechnologie mit Flammenstabilisierungsleisten und sorgfältige Vor-Ort-Bewertungen und -Anpassungen konnten die anfänglichen Nachrüstkosten sowie die langfristigen Wartungs- und Betriebskosten gesenkt werden.
Technisches Papier herunterladen