
Spezialität Thermische Oxidationsmittel
Systeme, die eine Zerstörungseffizienz von 99,9999 % erreichen
Säure Gas
Zeeco bietet sowohl Standard- als auch kundenspezifische Entsorgungslösungen für eine Vielzahl von Verbrennungsanwendungen in Gasanlagen, einschließlich der thermischen Oxidation von Abgasen aus Aminbehandlungsanlagen (saures Gas oder Abgas), Glykol-Dehydrationsdämpfen (BTEX) und SRU-Abgas.
ZeecoDie standardmäßigen thermischen Abluftreiniger sind kurzfristig zum Kauf oder zur Miete verfügbar und bieten die folgenden Funktionen:
Typische Leistung:
- Zerstörungswirkungsgrad (DRE) bis zu 99,9999%
- NOx emissions <30 ppm(vd) at 2% oxygen level
- NFPA 86-konformes Brenner Management System (BMS)
Typische Anwendungen:
- Amin-Behandler Saures Gas
- Glykolentwässerungsanlage/BTEX-Abgas
- SRU Endgas
- Tankentlüftungen
Gestaltungsmerkmale:
- Die Montage auf einem Gestell ist möglich: Keine aufwendige Verkabelung oder Verrohrung zwischen dem thermischen Abluftreiniger und dem Brennstoffregal
- 30' und 60' Standard-Stapelhöhen
- ZeecoAR/GS-1 HEI Pilotzündsystem - die Zündflamme kann auch dann gezündet werden, wenn sie komplett unter Wasser ist!
- Vollfarbige Touchscreen-Schnittstelle (HMI) mit integrierter Diagnose
- Mobiltelefon-Modem für Fernüberwachung und -unterstützung
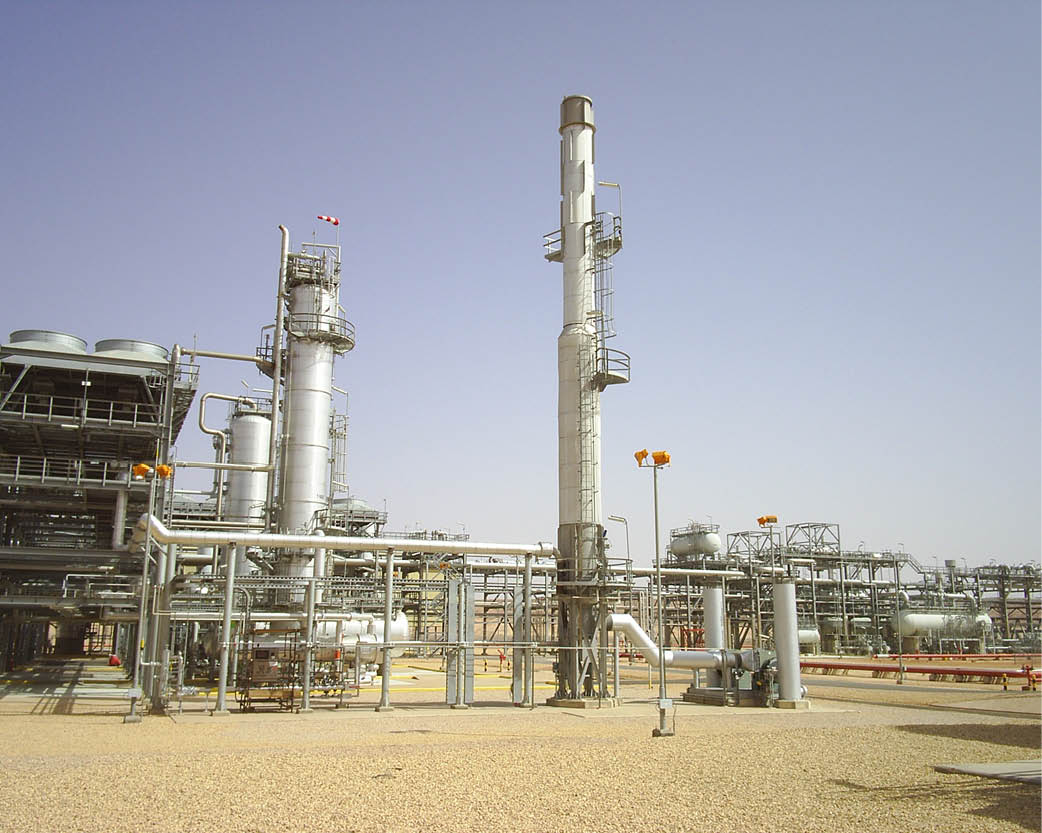
Erholsam
Typische Leistung:
- Hohe Zerstörungseffizienz (DRE): >99.9%
Typische Anwendungen:
- Heizölerhitzer
- Dampfkessel
- Luft- und Abgasvorwärmer
- Schwefeldienst
Gestaltungsmerkmale:
- Direkt befeuert
- Tolerant gegenüber Erschütterungen
- Für alle Abfallarten geeignet
- Keine beweglichen Teile oder Wärmetauschermedien
.jpg)
Heruntergebranntes Salz / Lauge
Nach unten befeuerte Verbrennungsanlagen behandeln in der Regel Abfälle, die anorganische Salze (NaCl, Na2SO4, Na2S), organische Salze (Acetate und Oxalate von Alkalimetallen), ätzende Flüssigkeiten und nicht brennbare Feststoffe enthalten. Nach unten gerichtete Verbrennungssysteme oder thermische Oxidationsanlagen verdanken ihren Namen den vertikal ausgerichteten Brennern, die sich am oberen Ende der Verbrennungsanlage befinden und nach unten feuern. Zeeco Die Konstruktion der Brenner ermöglicht eine längere Lebensdauer der Feuerfestmaterialien und bietet Raum für die Ansammlung von nicht brennbaren Feststoffen im Abgas. Viele Zeeco Verbrennungsanlagen mit nach unten gerichteten Brennern verfügen über zusätzliche Ausrüstungen wie Schlauchfilter, Multiklonfilter und Elektrofilter, um eine bessere Partikelabscheidung zu gewährleisten.
Typische Leistung:
- Verweilzeit = 2,0 Sekunden
- Betriebstemperatur = 1650 bis 2000°F (900 bis 1100°C)
- Effizienz der Abfallvernichtung (DRE) > 99,9999%
- Partikelemissionsraten = 0,005 bis 0,08 Körner/DSCF
Typische Anwendungen:
- Chemische Anlagen
- Petrochemische Anlagen
- Verbrauchte kaustische Abfallströme
- Organische/anorganische Salzlösungen
- Abfallströme von Holzprodukten
- Biomass-to-Energy-Verfahren
- Anwendungen für Katalysatoren
Gestaltungsmerkmale:
- Feuerfeste Materialien mit geringer Porosität, um den Salzangriff zu minimieren
- Die firmeneigene Konstruktion minimiert den Kontakt des geschmolzenen Salzes mit den feuerfesten Wänden, um eine maximale Lebensdauer des Feuerfestmaterials zu gewährleisten
- Proprietäre Konstruktion "friert" geschmolzene Salze vor dem Kontakt mit nachgeschalteten Wärmerückgewinnungs-/Partikelfilteranlagen ein
- Zu den Partikelabscheidern können Schlauchfilter, Multiklonfilter, Elektrofilter oder Venturiwäscher gehören.
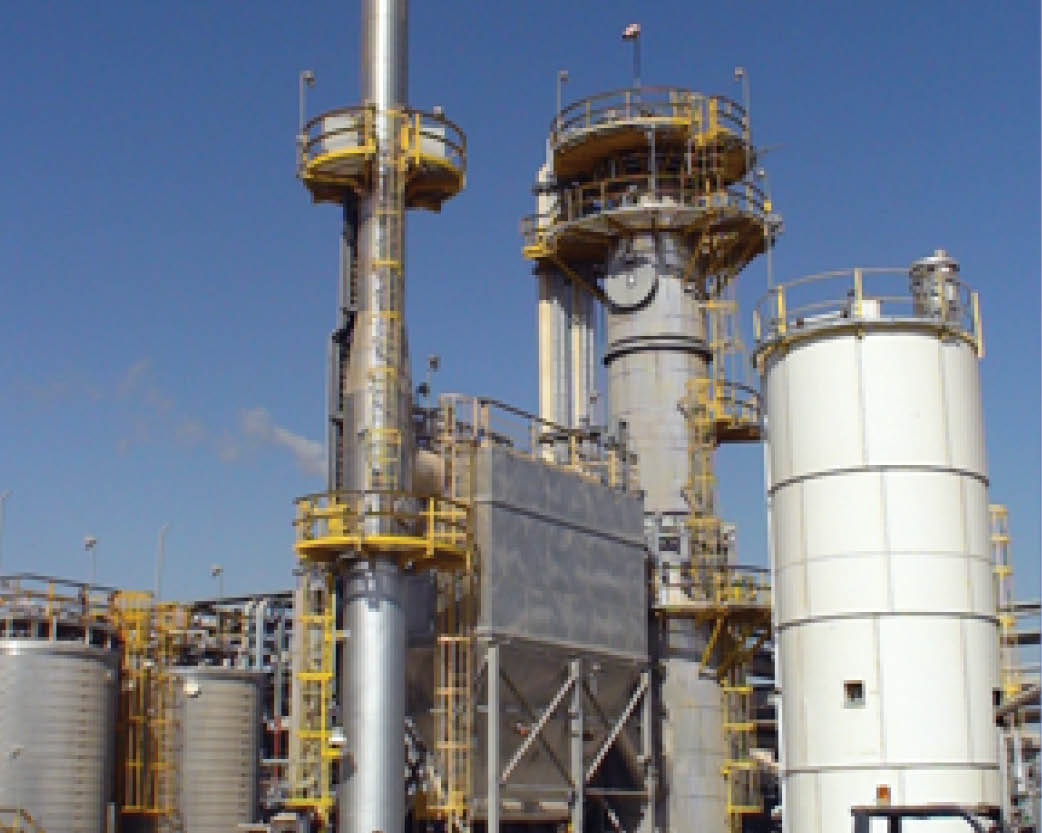
mehrstufig schadstoffarm
Bei der Hochtemperaturverbrennung von stickstoffhaltigen Abfällen in einer herkömmlichen Umgebung mit Luftüberschuss entstehen inakzeptable Mengen an Stickstoffoxidemissionen. Um die Bildung von NOx zu begrenzen, setzt Zeeco einen mehrstufigen Low-NOx-Verbrennungsprozess ein. ZeecoDie Erfahrung von mit thermischen Abluftreinigungsanlagen für stickstoffgebundene Abfälle umfasst Systeme mit einer Größe von 1,0 MMBtu/Std. (0,25 MMKcal/Std.) bis zu mehr als 450 MMBtu/Std. (114 MMkcal/Std.). Die Brennkammer kann einen Durchmesser von 4,0' (1,0 m) bis 18' (5,5 m) haben.
Typische Leistung:
- NOx emissions for Nitrogen Bound Waste Streams <100 ppm (vd)
- Abfallvernichtungseffizienz (DRE) > 99,99% (verfügbar bis zu 99,9999%)
Typische Anwendungen:
- Petrochemische Anwendungen mit Aminen, Nitrilen usw.
- Ammoniak- und/oder Zyaniddämpfe
- Schwefelrückgewinnungsanlagen: Sauerwasser-Stripper (SWS) Gasüberkopfströme
- Herstellung von Kohlenstofffasern LT/HT Off-Gas-Ströme
- Luftströme in der Elektronikfertigung
Gestaltungsmerkmale:
- Garantiert vorhersehbares Emissionsverhalten
- Ordnungsgemäße Wiederzündung in der Oxidationsstufe
- Brenner Die Verbrennungsluft wird für eine optimale Kontrolle effizient von der Verbrennungsabfallluft getrennt
- Zuverlässige Prozesskontrolle und langfristige Zuverlässigkeit
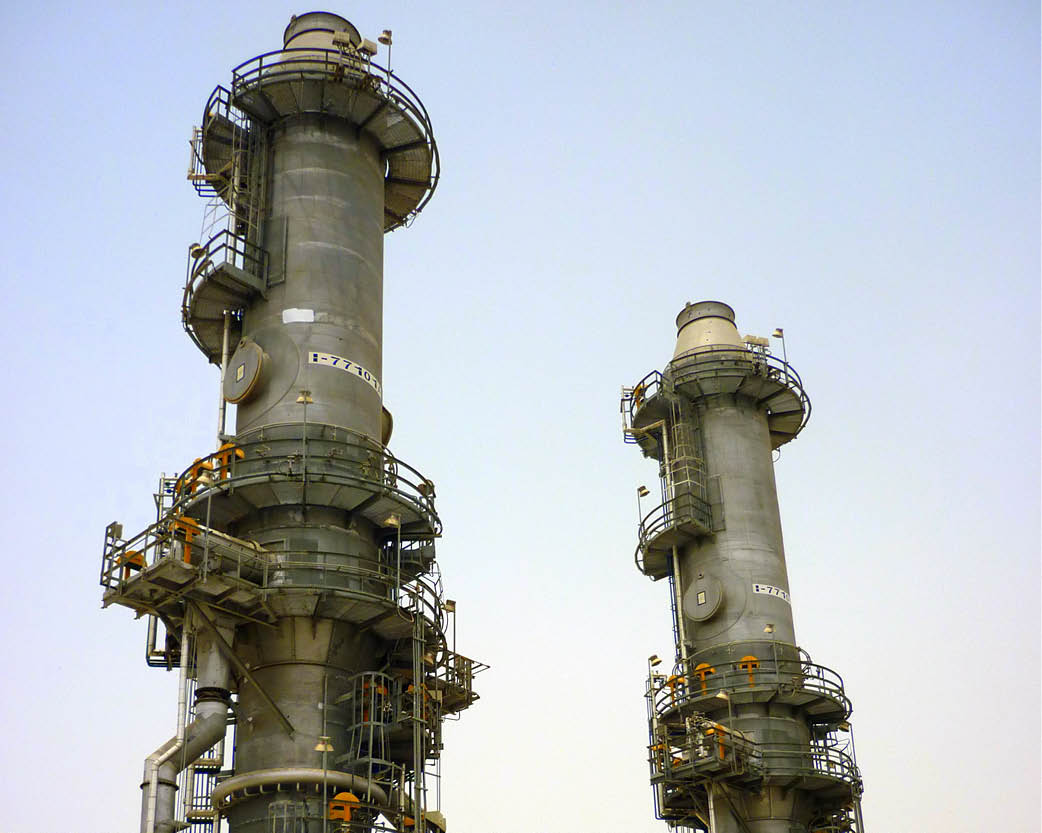
Kohlenmonoxyd
Kohlenmonoxidkessel sind thermische Abluftreiniger, die zur Oxidation von kohlenmonoxidreichen Abgasen eingesetzt werden, die typischerweise bei Fluidized Catalytic Cracking (FCC) und Residual Cracking (RCC) in Erdölraffinerien entstehen. Aufgrund der großen Dampfmenge, die durch ein integriertes Abwärmerückgewinnungssystem erzeugt wird, werden sie traditionell als "CO-Kessel" bezeichnet. Zeeco ist ein zugelassener Lieferant von Kohlenmonoxidkesseln für alle großen FCC/RCC-Prozessanlagen-Lizenzgeber der Welt.
Typische Leistung:
- Verweilzeit = 1,0 Sekunden
- Betriebstemperatur = 1850°F (1010°C)
- Effizienz der Abfallvernichtung (DRE) >99,9999%
Typische Anwendungen:
- Erdölraffinerien: Fluidisierte katalytische Krackanlagen (FCCU)
Gestaltungsmerkmale:
- Die maßgeschneiderte Konstruktion des thermischen Abluftreinigers garantiert eine optimale Emissionsleistung
- Bewährtes internes Abgaseinspritzsystem gewährleistet Flammenstabilität und ordnungsgemäße Zündung des Kohlenmonoxid-Abfallstroms
- Der systembasierte Ansatz bietet eine zuverlässige Prozesssteuerung und Zuverlässigkeit für das gesamte Verbrennungs- und Abwärmekesselpaket
- Das Design des feuerfesten Systems bietet Schutz gegen den Abrieb von Katalysatorpartikeln und hohe Betriebstemperaturen
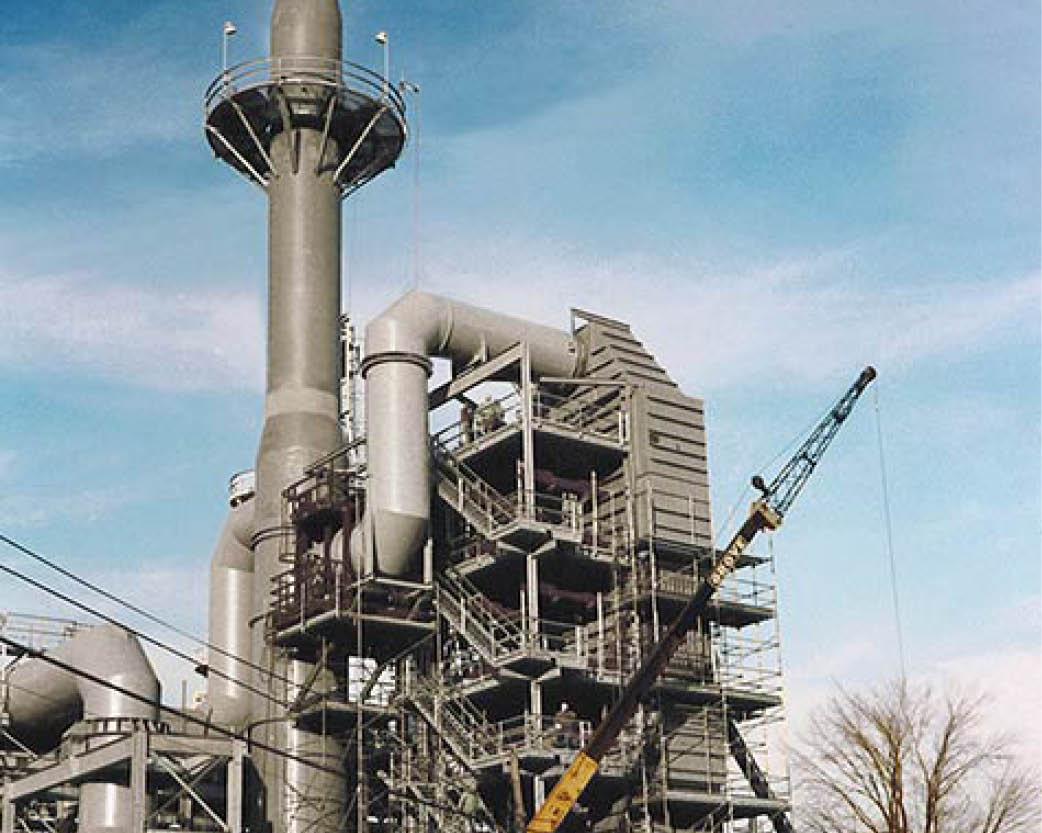
flüssige Abfälle
Flüssigabfallverbrennungsanlagen behandeln in der Regel Abfälle, die ein breites Spektrum an Wasser, Kohlenwasserstoffen und nicht brennbaren Feststoffen enthalten. Flüssigmüllverbrennungsanlagen oder thermische Oxidationsanlagen können horizontal oder vertikal befeuert werden. ZeecoDie Konstruktion von zeichnet sich durch eine längere Lebensdauer des Feuerfestmaterials sowie durch eine patentrechtlich geschützte Flüssigkeitsinjektionstechnologie für alle nicht brennbaren Feststoffe im Abfallstrom aus. Viele thermische Abfallverbrennungsanlagen von Zeeco verwenden zusätzliche Ausrüstungen wie Wäscher, Baghouses, Multiklonfilter, Elektrofilter und SNCR/SCR-Systeme, um eine verbesserte Emissionsreduzierung und Partikelabscheidung zu ermöglichen.
Typische Leistung:
- Verweilzeit = 1,5 - 2,0 Sekunden
- Betriebstemperatur = 1650 bis 2200°F (900 bis 1200°C)
- Effizienz der Abfallvernichtung (DRE) ' 99,9999%
- Erfüllt weltweit anerkannte Emissionsstandards
Typische Anwendungen:
- Chemische Anlagen
- Petrochemische Anlagen
- Verbrauchte kaustische Abfallströme
- Organische/anorganische Salzlösungen
- Abfallströme von Holzprodukten
- Biomass-to-Energy-Verfahren
- Anwendungen für Katalysatoren
Gestaltungsmerkmale:
- Feuerfeste Materialien mit geringer Porosität zur Minimierung von Salz- und Säuregasangriffen
- Proprietäres Design minimiert den Kontakt der Flüssigkeit mit den feuerfesten Wänden, um eine maximale Lebensdauer des Feuerfestmaterials zu gewährleisten
- Proprietäres Design der Flüssigkeitseinspritzdüsen verhindert Verstopfung
- Nachverbrennungsanlagen können Wäscher, Schlauchfilter, Multiklonfilter, Elektrofilter, SNCR-/SCR-Systeme oder Venturiwäscher umfassen.
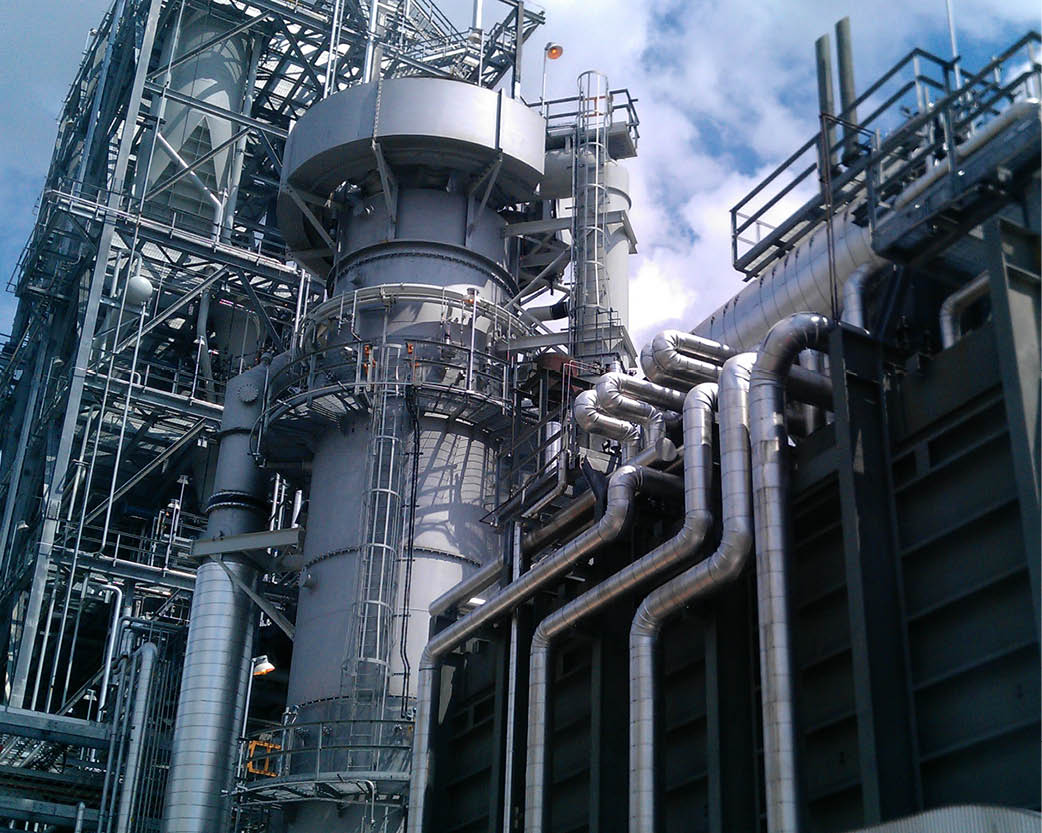
Halogenierte Kohlenwasserstoffe
Halogenierte Kohlenwasserstoffe sind solche, die Chlor, Brom, Fluor, Jod usw. enthalten. Chlor ist das am häufigsten vorkommende Halogen in Abfällen aus petrochemischen Anlagen. Vinylchloridanlagen verwenden in der Regel unsere Verbrennungsanlagen, aber Zeeco bietet eine breite Palette von Lösungen für alle gasförmigen und flüssigen Abfälle von halogenierten Kohlenwasserstoffen.
Typische Leistung:
- Verweilzeit = 2,0 Sekunden
- Betriebstemperatur = 1800 bis 2200°F (982 bis 1204°C)
- Effizienz der Abfallvernichtung (DRE) > 99,9999%
Typische Anwendungen:
- Vinylchloridmonomer (VCM) / Ethylendichlorid (EDC)
- Tetrachlorkohlenstoff (CCl4)
- Polyvinylchlorid Biphenyle (PCBs)
- Bromhaltige Abfallströme
Gestaltungsmerkmale:
- Für kleine Systeme mit geringen HCl-Mengen ist ein einstufiger Laugenwäscher in der Regel ausreichend, um die Umweltauflagen zu erfüllen.
- Für größere Systeme empfiehlt Zeeco einen zweistufigen Absorber/Wäscher, bei dem HCl als flüssiges Nebenprodukt zurückgewonnen werden kann
- Die Abwärmenutzung kann über einen Feuerrohrkessel erfolgen, der zwischen der thermischen Oxidationsanlage und der Füllkörperkolonne integriert ist.
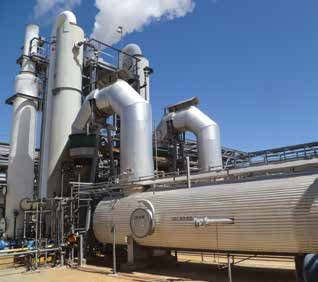
Unser Angebot an Dienstleistungen
MÄRKTE, DIE WIR BEDIENEN
Zeeco kann überall dort, wo Kohlenwasserstoffe verarbeitet werden, Lösungen zur Verbrennungs- und Emissionskontrolle anbieten. Unsere Kunden finden unsere Anlagen und Dienstleistungen in vor-, mittel- und nachgelagerten Öl- und Energieprozessen.
Wir bieten auch Produkte und Unterstützung für andere Branchen und Anwendungen, wie z. B. Tank-/Terminalbeladung und -lagerung, Pharmazie, Ruß, Zellstoff und Papier, Stahl, Lebensmittelverarbeitung und mehr.